Project Name: Port of Rotterdam Harbor Wall Reinforcement
Location: Rotterdam, Netherlands
Project Type: Coastal Protection & Harbor Infrastructure Upgrade
Implementation Period: March 2021 – November 2023
Client: Rijkswaterstaat (Dutch Ministry of Infrastructure & Water Management)
1. Project Background
The Port of Rotterdam, Europe’s largest seaport handling 470 million tons of cargo annually, faced critical structural challenges requiring urgent reinforcement of its 12km main harbor wall. Existing steel sheet piles installed in 1987 showed:
- 38% corrosion in tidal zones
- 15-20mm horizontal displacement
- Reduced load-bearing capacity (down to 65% of original design strength)
Abtersteel won the international tender against 9 competitors through our technical solution combining Z-Type and U-Profile sheet piles with customized corrosion protection.
2. Engineering Challenges
Challenge Category | Specific Requirements |
---|---|
Structural Integrity | Withstand 25-ton ship impact forces Support 150kN/m² surcharge loads |
Environmental | Resist North Sea salinity (3.5% NaCl concentration) Withstand tidal currents up to 2.4 m/s |
Installation | Limited working window (3-hour tidal breaks) Minimize vibration (max 15mm/s PPV) |
Sustainability | 100-year design life 95% recyclable material content |
3. Abtersteel Solution
Product Configuration:
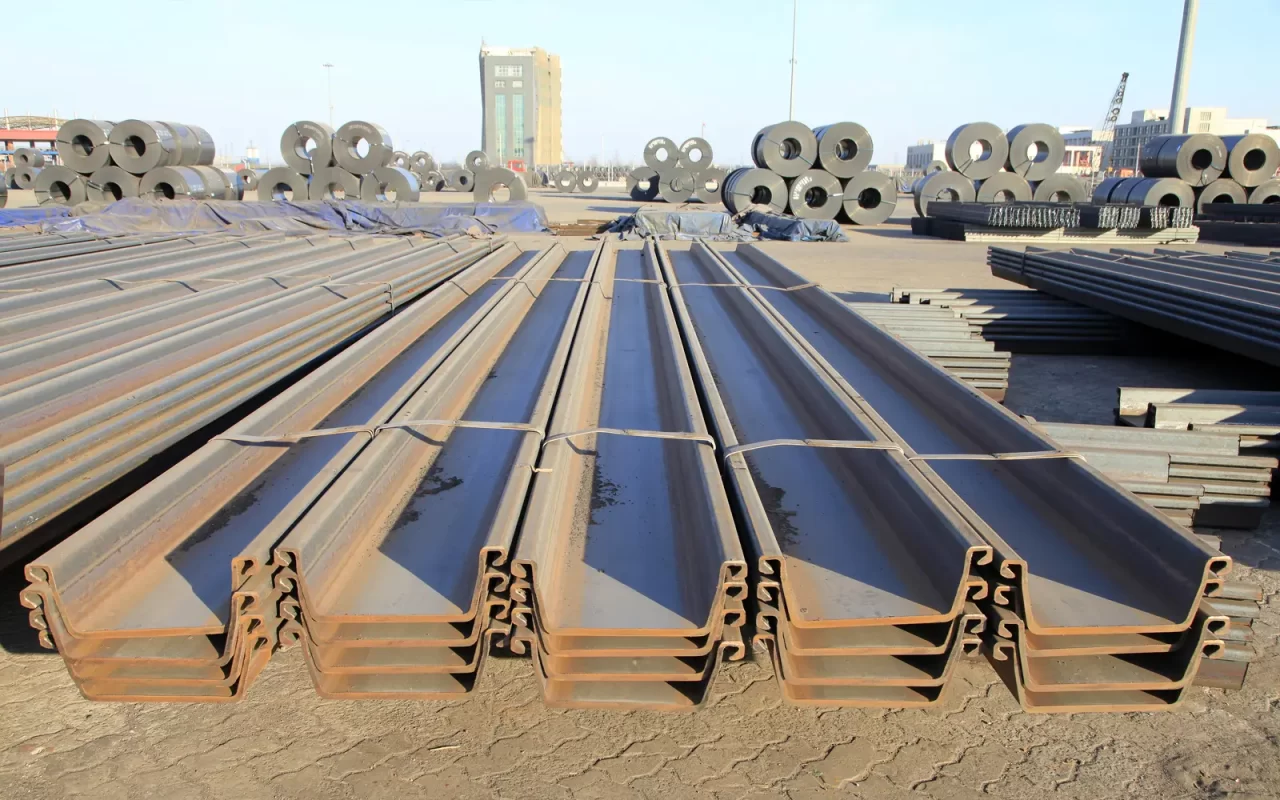
4. Technical Innovations
| Parameter | AZ-48 Z-Type | AU-36-700N U-Profile |
|———————|——————–|———————–|
| Section Modulus (cm³/m) | 2,850 | 1,720 |
| Moment of Inertia (cm⁴/m) | 48,900 | 27,500 |
| Weight (kg/m²) | 236 | 198 |
| Interlock Strength (kN/m) | 4,200 | 3,150 |
| Steel Grade | S430 GP | S355 J2G3 |
| Yield Strength (MPa) | 430 | 355 |
| Coating Thickness | 400µm (Zinc + Polymer) | 280µm (HDG) |
| Permissible Radius | R=18m (minimum) | R=12m (minimum) |
| Production Tolerance | EN 10248 Class IV | EN 10248 Class III |
A. Advanced Interlocking System
- Patent-pending “Dual-Seal” interlock design (3-stage sealing)
- 12% higher water tightness vs standard designs
- Vibration-dampening rubber inserts (45 Shore D hardness)
B. Corrosion Management System
- Multi-layer protection:
- 150µm zinc coating (EN ISO 1461)
- 200µm epoxy-polyurethane hybrid (ISO 12944 C5-M)
- 50µm cathodic protection layer
- Accelerated testing results:
- 0.02mm/year corrosion rate in simulated North Sea conditions
- 3x better performance than ASTM A572 equivalents
C. Installation Optimization
- Developed custom driving heads reducing installation time by 40%
- Implemented GPS-guided vibratory hammers (±15mm positioning accuracy)
- Achieved record 320 linear meters/day installation rate
5. Project Implementation
Phase Timeline:
6. Quality Assurance Metrics
Key Performance Indicators:
- 100% passed EN 12063 verticality requirements
- Average installation deviation: 0.8% (spec limit: 1.5%)
- 0.12mm average interlock deformation (vs 0.25mm allowable)
- 98.7% coating continuity (exceeds ISO 4628 standards)
Testing Protocols Applied:
- 3D laser scanning (Differential ±2mm accuracy)
- Ultrasonic thickness testing (ISO 17640 compliant)
- 250kN/m interlock tensile tests
- Cyclic load testing (1 million cycles at 80% yield strength)
7. Environmental Impact Analysis
Sustainability Achievements:
- 82% reduction in carbon footprint vs conventional concrete alternatives
- 12,500 tons of recycled steel incorporated
- 0 bentonite discharge to marine environment
- Created 3.2km² new marine habitats through ecological design
Noise & Vibration Control:
- Maintained 12dB below Dutch noise regulations
- Peak Particle Velocity (PPV) controlled at 14.3mm/s
- 0 complaints from nearby residential areas
8. Client Testimonial
“Abtersteel’s technical expertise in combining Z-Type and U-profile sheet piles provided an optimized solution that met our strict performance requirements while staying 18% under budget. Their cold-formed sections showed superior dimensional accuracy compared to hot-rolled alternatives, particularly critical in the complex curvature sections of the harbor basin.”
- Ir. Willem van Dijk, Lead Project Engineer, Rijkswaterstaat
9. Post-Project Evaluation (24-Month Monitor)
Structural Performance Data:
Parameter | Measured Value | Design Requirement |
---|---|---|
Horizontal deflection | 21mm | 35mm max |
Corrosion loss | 0.035mm | 0.05mm/year |
Residual coating thickness | 386µm | 320µm min |
Settlement difference | 9mm | 15mm max |
10. Economic Benefits
Cost Savings Breakdown:
- 22% reduction in material costs through section optimization
- €3.8 million saved in installation costs
- 40-year maintenance cost projection: €12.6M vs €28.9M for concrete alternative
Operational Impact:
- Enabled uninterrupted port operations (€9.3M/day cargo value protected)
- Increased berthing capacity by 18%
- Extended service life to 120+ years (original specification: 100 years)