Sheet piles are structural sections made of steel, concrete, or composite materials that are used in construction and civil engineering projects for various applications. They are designed to provide earth retention and excavation support, as well as to create permanent or temporary retaining walls and cofferdams. Here are some common types of sheet piles and their applications:
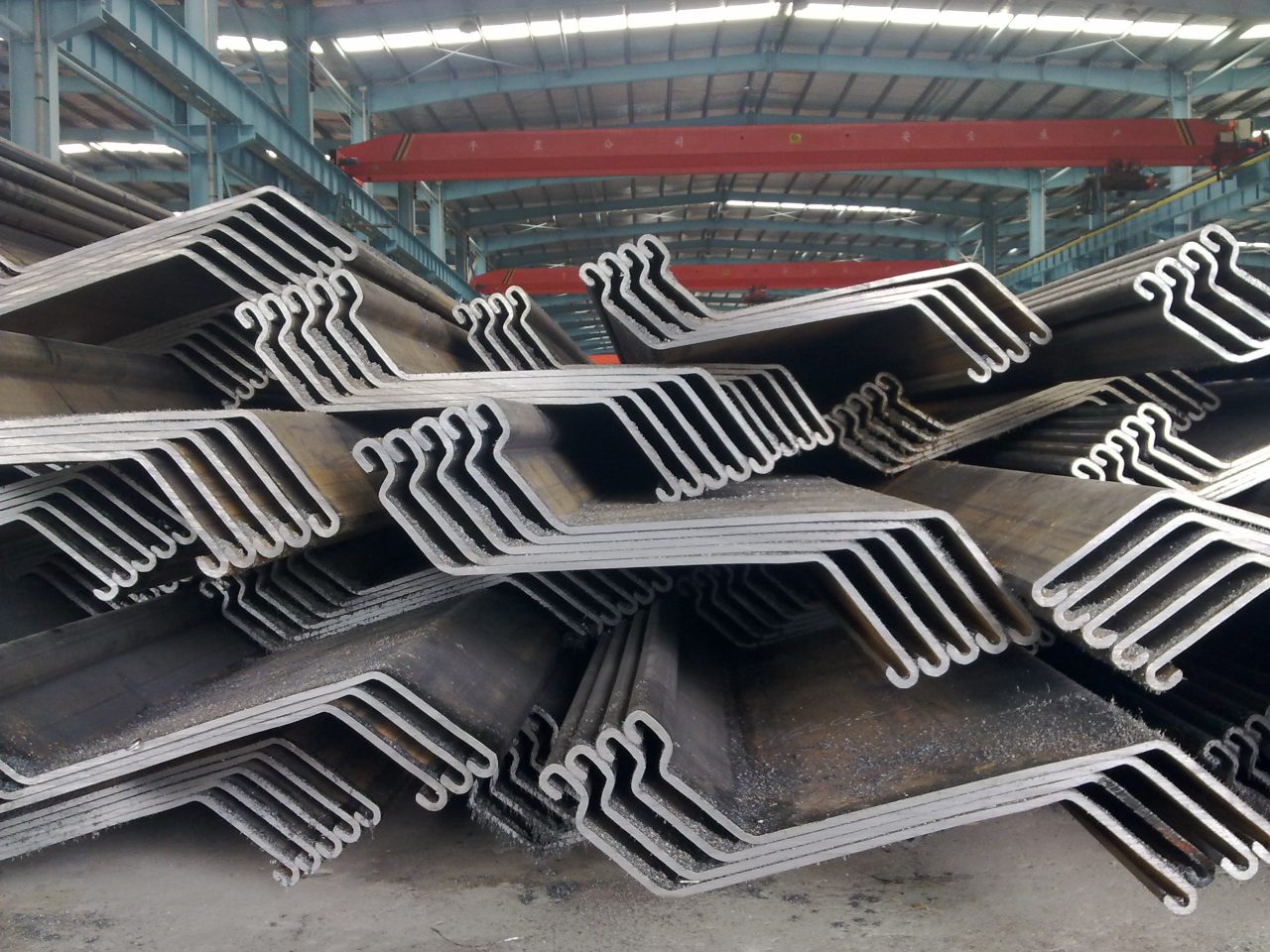
- Steel Sheet Piles: Steel sheet piles are widely used due to their strength, durability, and versatility. They are available in different shapes and sizes, including U-shaped, Z-shaped, and straight web sections. Steel sheet piles are commonly used in the following applications:
- Retaining walls: Steel sheet piles are used to create permanent or temporary retaining walls in construction projects such as basements, underground structures, and waterfront developments.
- Cofferdams: They are used to create temporary enclosures to allow construction work in dry conditions, such as bridge piers, dams, and deep foundation excavations.
- Flood protection: Steel sheet piles are used to construct flood control barriers and embankments to protect against rising water levels.
- Concrete Sheet Piles: Concrete sheet piles are precast and reinforced with steel bars. They offer excellent durability and resistance to corrosion. Concrete sheet piles are commonly used in the following applications:
- Marine structures: They are used in the construction of seawalls, breakwaters, jetties, and other marine structures to provide erosion control and shoreline protection.
- Cut-off walls: Concrete sheet piles are used as cut-off walls to prevent the seepage of water or contaminants in areas such as landfills, reservoirs, and underground storage tanks.
- Deep excavation support: They are used to provide temporary support during deep excavations for basements, underground parking, and tunnels.
- Composite Sheet Piles: Composite sheet piles are made of a combination of materials, such as fiberglass and polymer composites. They offer advantages such as lightweight, corrosion resistance, and ease of handling. Composite sheet piles are commonly used in the following applications:
- Environmental barriers: Composite sheet piles are used in the construction of containment barriers, such as for landfills, hazardous waste sites, and contaminated soil remediation projects.
- Landscaping and erosion control: They are used in landscaping projects, riverbank stabilization, and erosion control applications.
- Temporary works: Composite sheet piles are suitable for temporary applications where cost-effective and lightweight solutions are required.
These are just a few examples of sheet pile types and their applications. The specific choice of sheet pile type depends on factors such as soil conditions, required load-bearing capacity, water levels, and project specifications. Consulting with a qualified engineer or contractor is recommended to determine the most appropriate sheet pile type for a specific project.
Cold Formed & Cold Rolled Sheet Piles
Cold Rolling and Forming processes are when the steel sheet pile is profiled at room temperature. The profile thickness is constant along the width of the profile. Typically, cold rolled/formed sheet piles are produced to BS EN 10249 Part 1 & 2. Cold Rolling occurs in a continuous section from hot rolled coil whereas Cold Forming occurs is discrete lengths either from decoiled hot rolled coil or plate. A wide range of widths and depths are achievable.

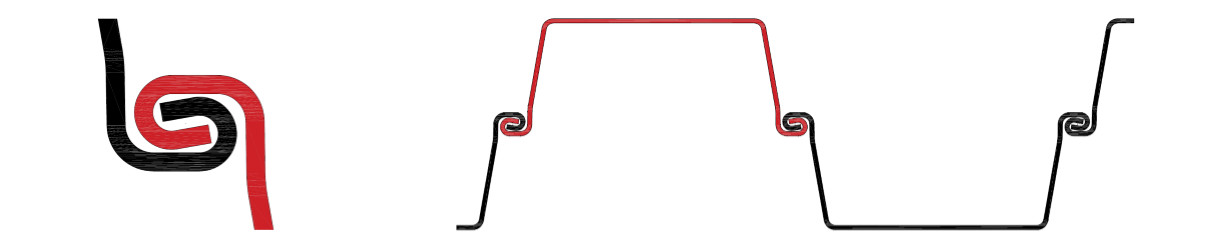
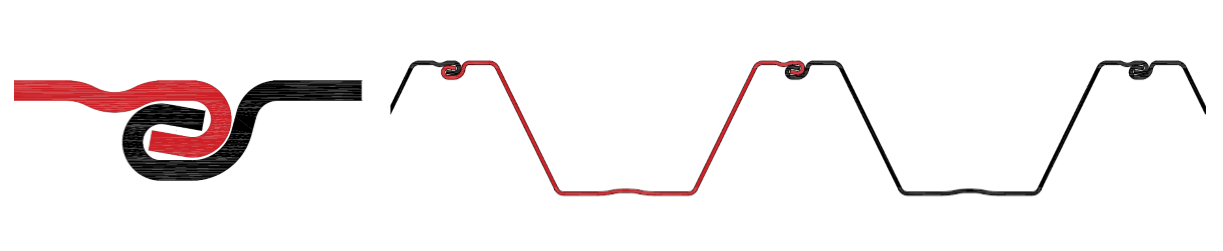
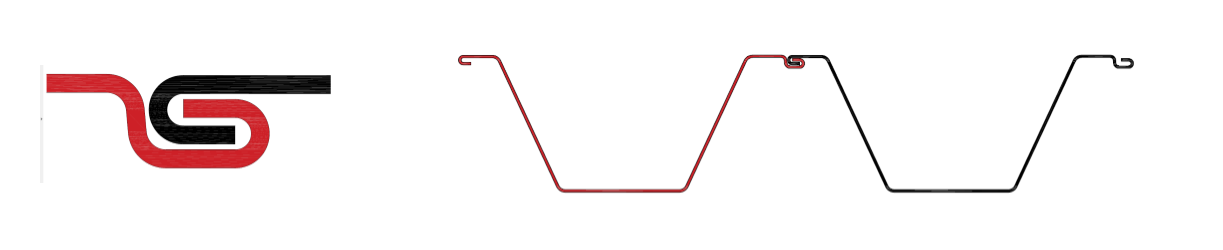
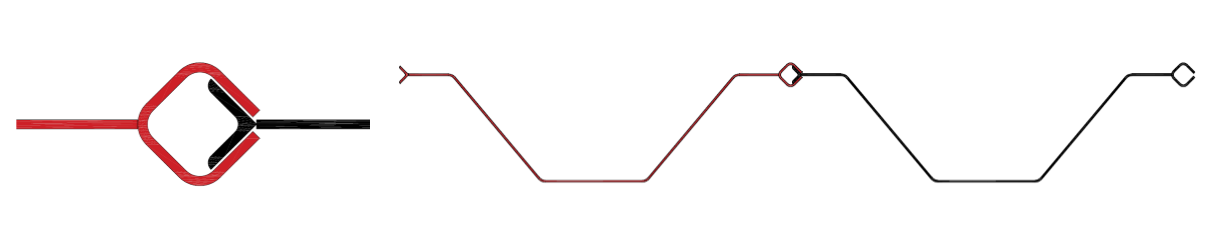
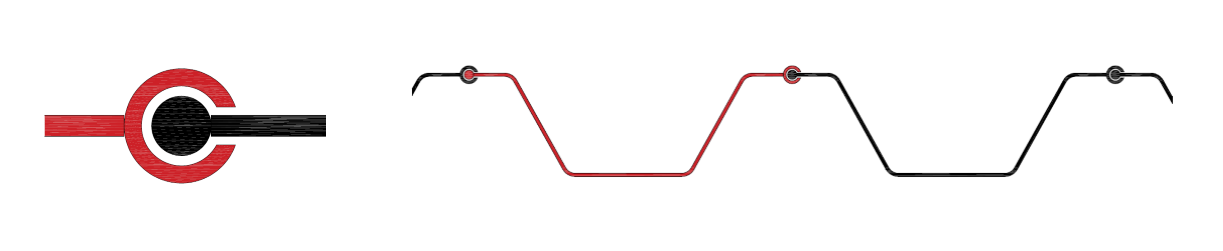
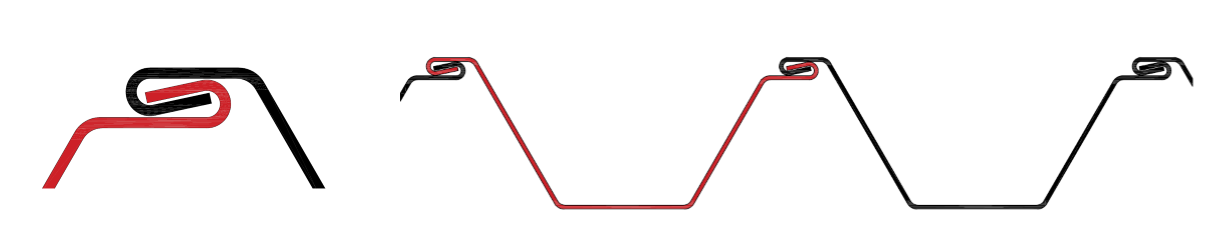
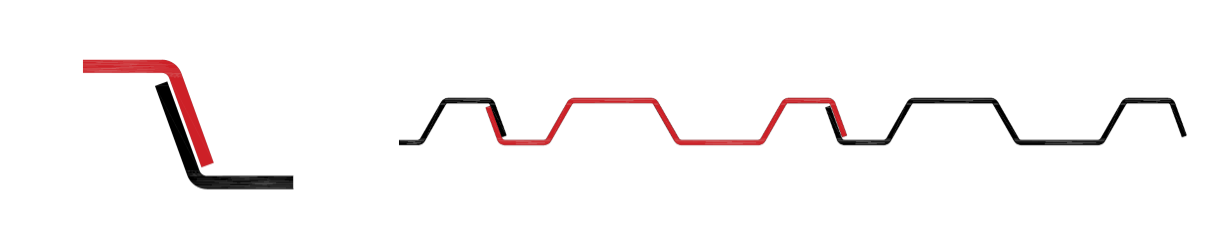
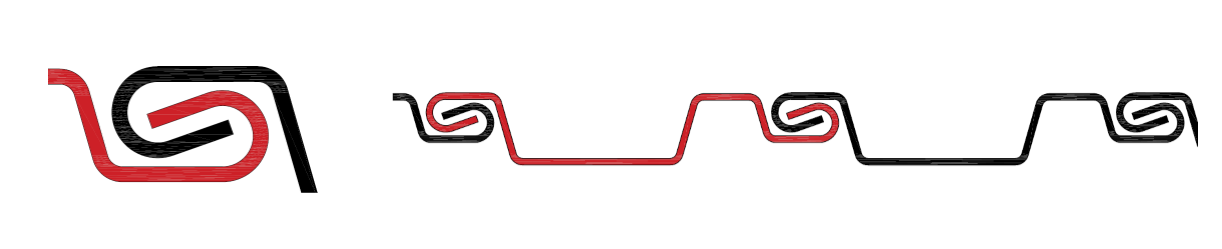
Indeed, Cold Rolling and Cold Forming are two key processes used in the manufacturing of steel sheet piles. Both these processes have their unique characteristics and applications.
Cold Rolling
Cold rolling is a process where the steel is worked at room temperature. This method tends to increase the strength of the steel by as much as 20% (or even more), mainly due to strain hardening, which is the result of the plastic deformation of a ductile material. Cold rolling can also improve the surface finish and hold tighter tolerances than hot rolling.
The process begins with hot rolled coil, which is uncoiled and passed through a set of two rolls, which reduce the thickness and increase the length. The steel sheet is then coiled up again and ready to be used.
As you mentioned, cold rolling occurs in a continuous section and the resulting products are typically produced to meet the BS EN 10249 Part 1 & 2 standards. The profile thickness remains constant along the width of the profile.
Cold Forming
Cold forming, on the other hand, involves shaping steel at room temperature by bending, drawing, or stamping. The process is performed in discrete lengths, either from decoiled hot rolled coil or plate. Cold forming provides a wider range of widths and depths, offering greater flexibility for different applications.
Cold forming is a popular method for the production of sheet piles as it allows for the creation of complex shapes with excellent dimensional precision.
Both cold rolling and cold forming result in increased hardness and strength of the steel due to the work hardening during the deformation process. However, these processes also increase the steel’s brittleness, which is why it’s crucial to balance the level of deformation with the application requirements of the end product.
While both processes can produce high-quality steel sheet piles, the specific choice between cold rolling and cold forming would depend on the specific requirements of the project, such as the desired shape, size, strength, and cost-effectiveness.
Hot Rolled Sheet Piles
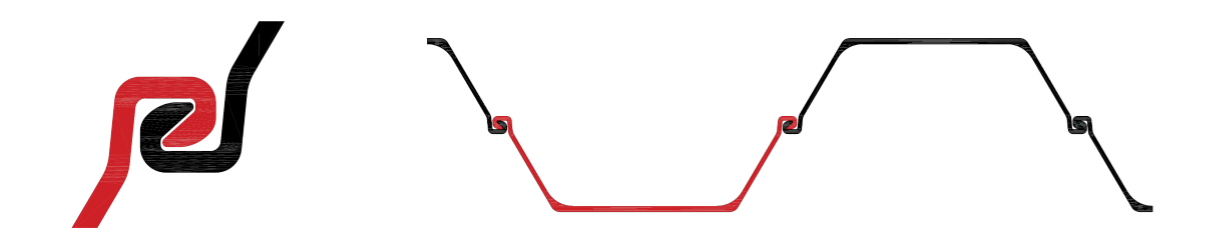
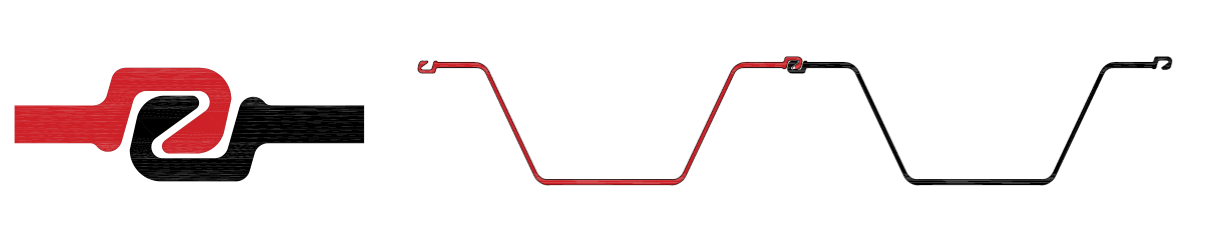
